Abstract:
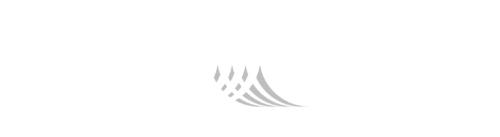
With growing electrification of light-duty vehicles, fast and super-fast (or high-power) charging stations for electric vehicles will be instrumental to continue enabling this transformation. In addition to plug-in charging, high-power wireless charging has been attracting increasing attention and interests. Despite the fact that wireless super-fast charger is highly efficient (above 90%), the amount of wasted energy it releases is still considerable. For instance, for a 1MW wireless charger under investigation, the expected heat dissipation rate will be minimum of 50 kW. Meanwhile, due to the compactness of these power electronics, the resultant heat flux (i.e., 25 kW/m2) will be challenging for conventional air-cooling solutions. In this study, thermal management of wireless supercharger module of electrical vehicle using a finned base heat sink integrated with Phase Change Material (PCM) has been investigated. Specifically, paraffin RT70 has been numerically investigated to study its feasibility as the desired PCM. A 2D model of the PCM domain has been developed in ANSYS Fluent, followed by simulations under high heat flux condition (i.e., 25 kW/m2). Given control of the junction temperature of power electronics is crucial to keep the system working efficiently and reliably, alternative PCMs and conduction enhancement techniques using different finned base heat sink configurations have been applied to achieve improved thermal management performance. Meanwhile, the effect of using PCM with different thermal conductivity has been studied to have a better understanding of its effect on the efficiency of thermal management system. In the end, the minimum surface temperature of the power electronic component for each configuration of finned base heat sink integrated with different types of PCMs has been presented and compared.
See publication:
--This publication pertains to:
Charging StationsPublication Authors:
- Mahdi Ghorbani
- Hailei Wang
- Nicholas Roberts